A secondary battery mixing process optimized for precision, durability, and sustainability.
Based on Jeil M&S's unique engineering expertise, we provide precise measurement and control technology to accurately manage and monitor raw material transfer volumes. We also ensure meticulous material selection to prevent raw material composition from being affected by contact with piping. Additionally, we design the entire process to flexibly adapt to changes in raw materials.
Process Overview


The secondary battery mixing process is composed of a fully automated line from raw material input to slurry supply for the coating process. Quality checks and change management at each stage of the process are critically important.
Technical Advantages
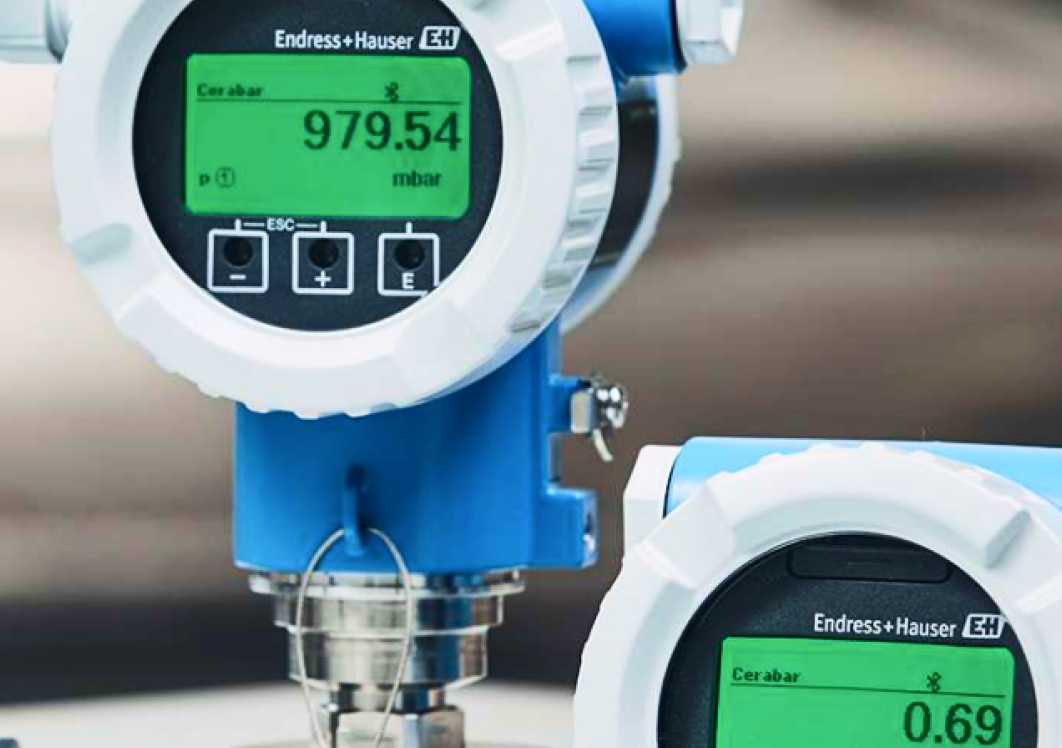
Real-Time Quality Measurement System
In conventional electrode slurry production processes connected by continuous closed-loop piping, workers manually measure slurry quality at each stage to prevent defective products from proceeding to the next step. Jeil M&S has significantly improved production efficiency by implementing a real-time continuous quality measurement system within the pipeline, eliminating the need for time-intensive manual inspections.
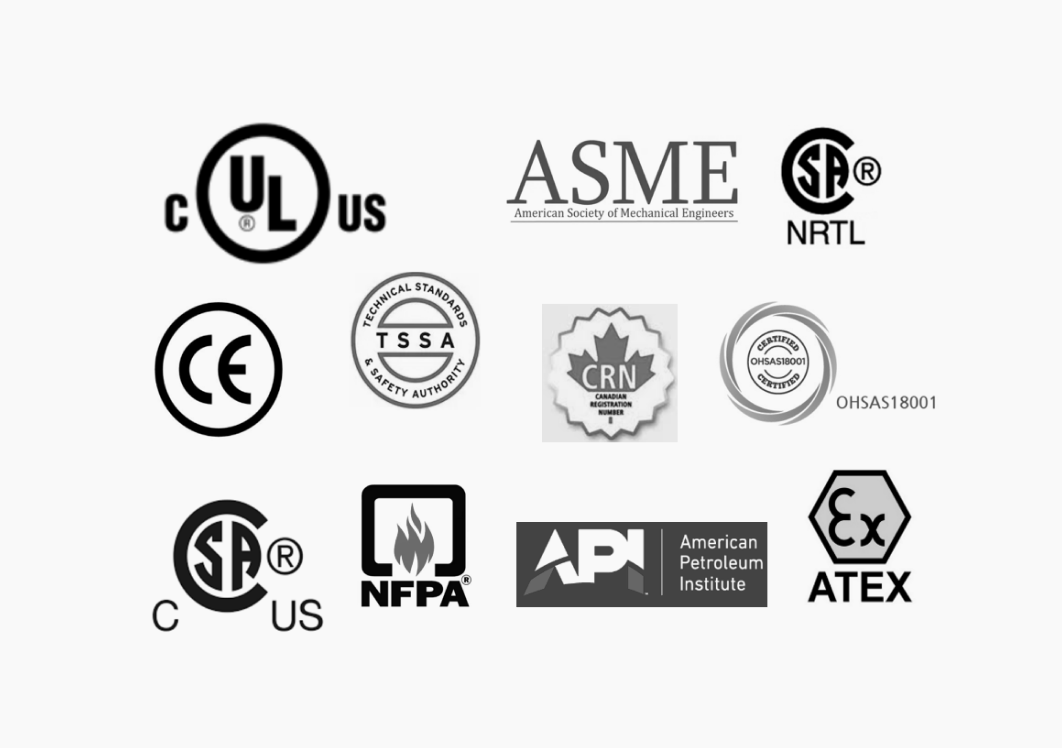
Dust Generation and Explosion Prevention Technology
Raw materials used in electrode production are divided into powdered and liquid forms. For powdered materials, friction during transfer, storage, weighing, and supply processes can lead to dust explosions. Ensuring worker safety from fine powder leaks is crucial, and we comply with international regulations to prevent such hazards. We complete the design, manufacturing, and installation processes to meet these standards.
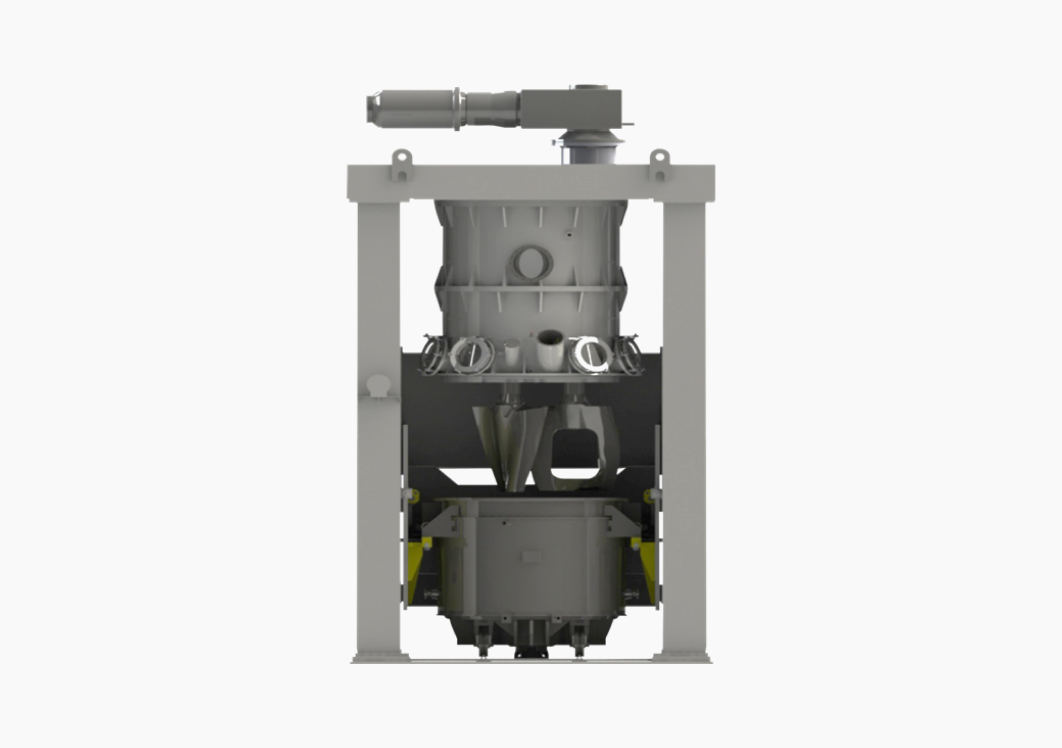
Optimal Mixing Blades and Unit Productivity Enhancement Technology
As the performance and productivity of secondary batteries improve, solid content levels continue to rise, increasing batch production capacities of main mixers. Ensuring productivity and durability in mixing equipment has become vital. Jeil M&S has developed ultra-high viscosity slurry mixing technology from the defense sector, allowing for proactive adaptation to higher solid content. This technology is applied to high-capacity main mixers in mass production lines.
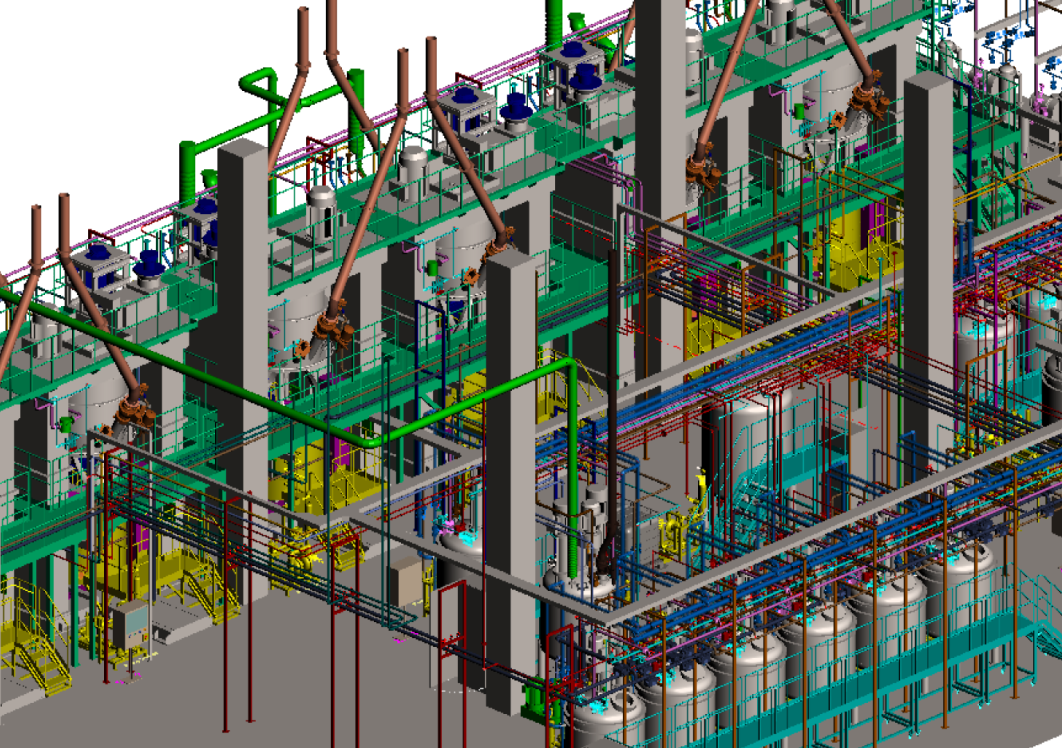
3D Modeling for
Pre-Installation Interference Checks
The secondary battery mixing process consists of complex piping and ducts connected to various equipment. To prevent construction delays due to interference during installation, Jeil M&S uses 3D modeling to pre-identify and eliminate potential conflicts between components.
Process Details
- STEP 1Raw Material Transfer and Storage
Active materials, binders, conductive agents, and solvents for cathode and anode materials are received and stored in hoppers via various transfer methods.
- STEP 2Weighing
Different raw materials required for anode and cathode slurries are automatically weighed according to recipe specifications and supplied to the mixer.
- STEP 3Pre-Mixing
Time-intensive processes, such as mixing binders or conductive agents, are conducted in advance and stored. These are then supplied to the main mixer as required.
- STEP 4Mixing
The main mixing process for electrode manufacturing, where binders, active materials, conductive agents, and solvents are mixed to produce slurry.
- STEP 5Slurry Storage
Slurry produced by the main mixer is stored or buffered in this stage.
- STEP 6Coater Supply
The stored slurry is supplied to the coater in amounts required for the coating process via supply tanks.